Types of motorcycle clutches
Clutch is a fairly obvious element of motorcycle design. It may seem that its only function is to allow for smooth starting and gear changes. Indeed, these are its main functions, but at the same time, the way it works can also affect riding comfort, engine smoothness, performance, and even motorcycle handling.
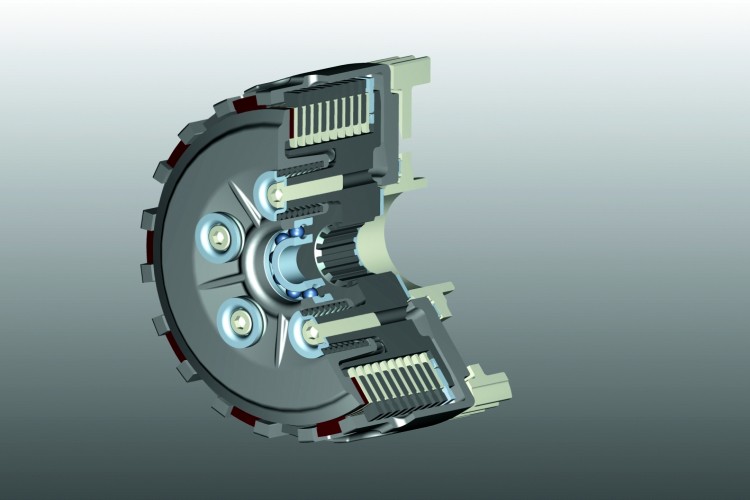
The engine and gearbox are two separate mechanisms that cannot be permanently connected to each other. If this were the case, changing gears would be much more difficult, and the drive would be constantly transmitted to the rear wheel, which no one would want. That is why a mechanism is needed between these elements that allows them to be connected and disconnected. This mechanism is, of course, the friction clutch.
Perfect synchronization
The first motorcycle clutches had little in common with those used today. They took on various forms, such as belt tensioners, but when in the 1920s motorcycles began to develop decent performance, the standard became a multi-plate clutch, which still reigns supreme today. Its main elements are two clutch baskets. The first, also known as the clutch hub, is mounted on the splines of the gearbox shaft. The outer basket is also mounted on this shaft but on a bearing. It is driven by the crankshaft - either through gears or with the help of a chain.
Each of these baskets is equipped with a set of plates. In the case of the hub, these are metal plates, while in the outer basket, friction plates are used. In order to enable movement and further driving, the friction plates must "engage" with the metal plates, so that the drive from the crankshaft can be transferred to the hub, and consequently to the gearbox shaft. When the drive is disconnected, for example when the clutch lever is pressed, the clutch pushrod moves the friction plates and metal plates apart. Or rather, it moves the pressure plate equipped with springs.
From cork to Kevlar
The multi-plate design has had no serious competitor for over 100 years, and there is nothing surprising about it. Such a clutch can very effectively transfer a large torque, and, unlike a single-plate car clutch, is small and light. Over all these years, the principle of its operation has not changed significantly, but the materials have, which has allowed for some reduction in the rotating mass, i.e. the mass that is strongly felt. However, the most important development was the use of materials for the friction plates. Initially, it was simply cork, which was sufficient when engines were neither powerful nor high-revving. As performance increased, cork was no longer able to maintain sufficient traction, and clutch slippage appeared. Another problem was the low durability of such plates.
Therefore, today clutch plates with a friction surface made of fiberglass or Kevlar composites are used. The latter are most often found in high-performance engines, where high durability and reliable, quick power transfer are needed. A curious fact is that some clutches used in speedway motorcycles have a friction surface made of a hard and adhesive material, very similar to rubber. Such plates "stick" to the spacers extremely quickly and transmit power without any slippage, which is of enormous importance in speedway. However, this solution is not resistant to prolonged use, especially at high temperatures, so it would not work well in other applications.
Pressing, but not too much
The precision and slip-free operation of the clutch also depend on the springs and pressure, which press the plates and spacers against each other after the pushrod is retracted. In theory, the stiffer the springs, the stronger the pressure and the greater the grip. On the other hand, very hard springs will provide too much resistance, making it a significant challenge for the left hand to operate the clutch, especially if it is operated by a cable.
A single-disk dry clutch has many advantages, but it is too large for transverse engines.
When it is necessary to use high stiffness springs, it is worth giving up the cable in favor of hydraulics. This makes the lever much lighter to operate and the clutch much more precise to control. Such control is based on a hydraulic pump, structurally identical to a brake pump, and on a clutch slave cylinder mounted on the pushrod. This, of course, raises the level of complexity of the construction, and consequently, the cost, but in higher-end models or high-performance machines, it is a cost worth paying. In the case of motocross, enduro, and trials, where clutch operation is almost constant, hydraulics are already practically a standard, precisely because of their light and precise operation.
KTM has developed an interesting solution to reduce left-hand fatigue. Initially in MX/enduro, and now in almost every model, they have abandoned traditional coil springs in favor of a single diaphragm spring. Thanks to this, the pressure is distributed more evenly, and clutch operation is much easier and more precise. Interestingly, in some variants, the spring tension can be adjusted, and thus the clutch characteristics, for example, to work a little slower and lighter, which is useful on very slippery and technical enduro sections.
Dry and wet
Excluding a few minor details, the construction of a multi-plate clutch is seemingly always the same. Two types can be distinguished, differing in the conditions under which they work. We are talking about a dry or wet version. The former, as the name suggests, works dry, without any lubricating or cooling liquid. Such a clutch is mainly used in racing constructions, where the torque is enormous and transmitted in a brutal way, but for a relatively short time.
Dry clutches perform excellently in such conditions, due to the immediate traction achieved between the discs and plates. They are extremely rare in road machinery, and today no manufacturer uses them, except for Moto Guzzi. However, they used to be a trademark of Ducati, which could be heard from afar. A dry clutch produces a characteristic rattling sound, natural for the operation of such a mechanism. Operating it in urban traffic is not precise or light. Not only does it work hard, but its operation culture is also quite low.
A slight bend in the disc or basket is enough to forget about the functional clutch.
It is definitely easier to live with a wet clutch, which works in an oil bath, shared with the gearbox. Thanks to constant lubrication, its operation is not only much lighter but also quieter. Oil simply muffles the sounds made by the clutch basket, springs, or rubbing plates and discs. Another advantage is the greater durability of this type of clutch and its resistance to overheating, due to constant cooling and lubrication. With all this, modern high-quality wet clutches in any engine that does not come from MotoGP do an excellent job of transmitting power smoothly and instantaneously. In addition, working in oil does not complicate the design, as channels in the baskets through which oil will flow are sufficient. It is not surprising, therefore, that dry clutches have disappeared from new motorcycles.
Single-plate clutches
For many years, two brands did not follow the trend of multi-plate clutches - BMW and Moto Guzzi. The standard equipment for boxer and longitudinal V2 engines was a single-plate dry clutch, modeled after a car. Due to its weight and large dimensions, with relatively poorer efficiency than multi-plate solutions, BMW eventually moved away from one disc. Today, only Moto Guzzi uses them. And if we are talking about exceptions to the rule, we will also find them in scooters. There, due to the presence of a continuously variable transmission, a centrifugal clutch is used. It has the form of arms with friction surfaces mounted on springs of a specified hardness. After exceeding specific speeds, thanks to centrifugal force, they are pressed against the so-called bell, allowing the transmission of power.
A diaphragm spring makes it easier to operate the clutch, provides even pressure, and allows for adjustment of the clutch's characteristics. In addition, such a set is known for its very high durability.
However, the latest clutch innovation, anti-hopping, is definitely not an exception to the rule. This solution significantly increases safety while allowing for much more effective control of the motorcycle (in sport). Thanks to it, during rapid gear reduction and rapid increase in revs, the rear wheel does not lock or jump. And this jumping can be really dangerous, especially as it can reach a frequency of even 15 times per second. In such a situation, the torque from the wheel side is higher than from the engine side, hence the wheel lock.
When a motorcycle is equipped with anti-hopping, in the event of such a situation, the clutch is immediately disengaged. This is possible thanks to dividing the clutch hub into two parts, between which control elements such as guides are placed. Thanks to them, in a crisis situation, the hub separates and the clutch works like a free wheel in a bicycle or simply both elements work independently of each other. In the past, this solution was used only as a tuning element or in a few sports motorcycles. Nowadays, it can be found in many new models, sometimes even in the 125 class.
At present, anti-hopping is the clutch hit of recent years and there is no sign of the situation changing significantly. Modern designs seem to be almost perfect and it would be difficult to replace them with anything else.